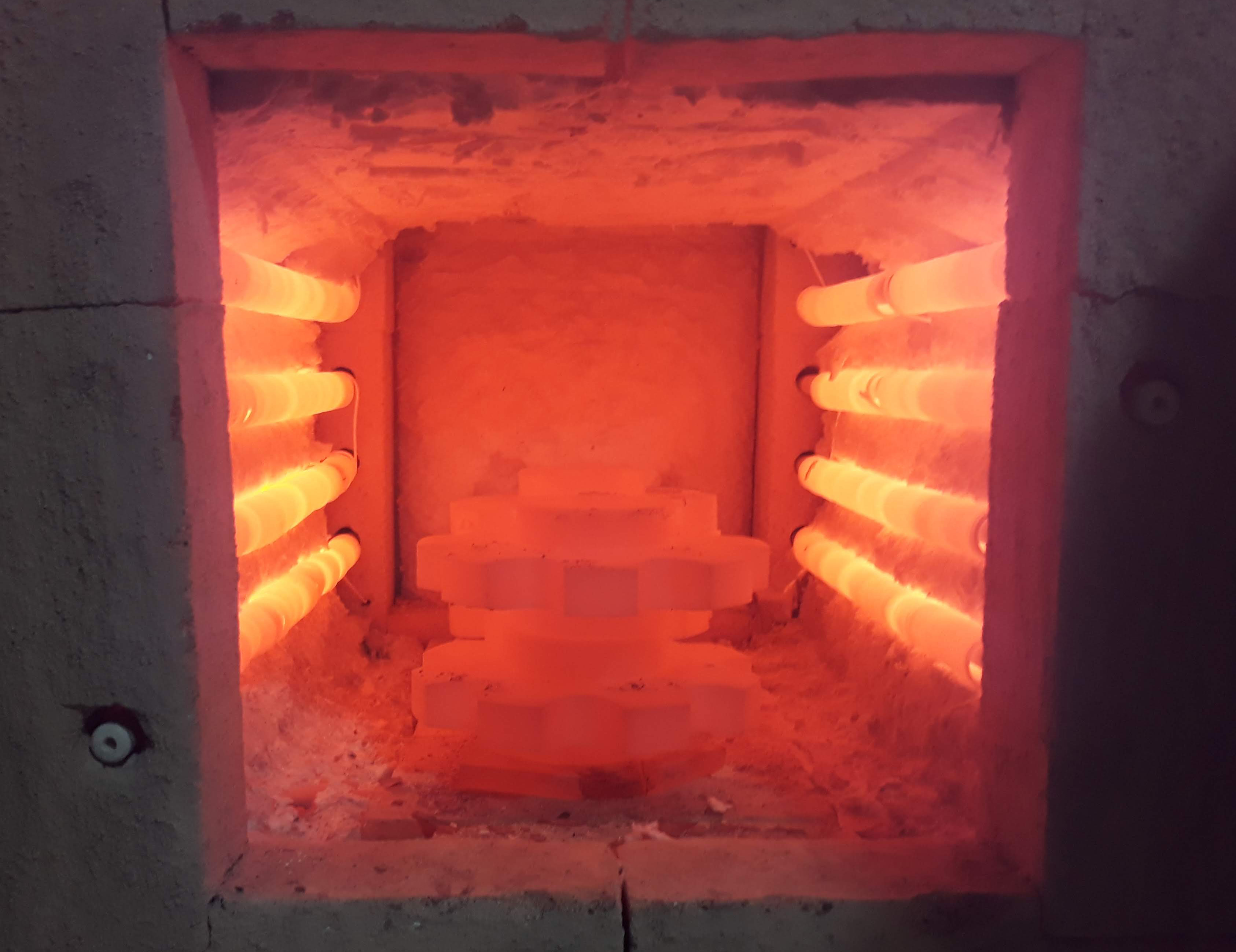
Термическая обработка
Термообработка стали – это технологический процесс, получения деталей из стали и сплавов с заданными качествами. Термообработку используют не только применительно к сталям, но и к цветным металлам и сплавам на их основе. Стали без термообработки используются лишь для возведения металлоконструкций и изготовления конструкционных деталей, срок службы которых невелик. К ним не предъявляются дополнительные требования. Повседневная же эксплуатация наоборот диктует ужесточение требований, именно поэтому применение термообработки предпочтительно особенно в области машиностроения.
Термической обработкой стали определяют процесс, состоящий из нагрева стальных заготовок (деталей), до определенных температур, выдержки и последующего охлаждения с заданной скоростью в определенной среде, с последующим отпуском. Основное назначение закалки - получение стали с высокими твердостью, прочностью, износостойкостью и другими свойствами.
Нагрев / Выдержка
Эта операция очень ответственная. От её правильного проведения зависит качество изделия. Процесс нагрева предусматривает применение камерных печей, которые могут нагревать среду до температуры 800-1300 градусов Цельсия и поддерживать ее на протяжении длительного периода. Это позволяет продлить время закалки стали и повысить качество получаемых заготовок. Отдельная технология разрабатывается для случая, когда заготовка имеет тонкие стены и грани. Представлена она поэтапным нагревом. Зачастую технология поэтапного нагрева предусматривает достижение температуры 500 градусов Цельсия на первом этапе, после чего выдерживается определенный промежуток времени для обеспечения равномерности нагрева и проводится повышение температуры до критического значения.
Температура нагрева при закалке зависит от марки стали, содержания углерода и выбирается по табл.
(чем меньше в стали содержание углерода, тем выше температура нагревания.)
Содержание углерода, % |
0,5 |
0,6 |
0,7 |
0,8 |
1 |
1,5 |
Температура, град |
830 |
815 |
800 |
780 |
770 |
770 |
Стали марок Ст.1, Ст.2, Ст.3, 10 и 15 не закаливаются из-за незначительного содержания углерода.
Для проведения любого теплового процесса термической обработки нужно не только нагревать металл до заданной температуры, но и выдерживать при этой температуре до полных структурных превращений (растворения карбидов, гомогенизации аустенита) и полного прогрева деталей. Таким образом, общее время пребывания деталей в нагревательной среде состоит из времени нагрева и времени выдержки.
Выдержка изделия при температуре закалки необходима для выравнивания температуры по всему сечению и обеспечения завершения происходящих при этом структурных превращений. Продолжительность выдержки зависит от сечения деталей и теплопроводности металла.
По среднему время нагрева заготовки определяется из расчета 1,5 мин на 1 мм диаметра или толщины детали.
Нагревательные устройства |
Температура нагрев,°С |
Время нагрева (сек.) 1 мм диаметра или толщины деталей с сечением |
||
круглым |
квадратным |
прямоугольным |
||
Электрическая печь |
800 |
40-50 |
50-60 |
60-75 |
|
|
|
|
|
Пламенная печь |
800 |
35-40 |
45-50 |
55-60 |
|
1300 |
15-17 |
17-19 |
19-22 |
|
Время выдержки при заданнойтемпературе tв можно упрощенно принять равным 1 мин для углеродистых сталей и 1,5 - 2 мин для легированных сталей.
Охлаждение.
Основной охлаждающей жидкостью для стали является вода. Если в воду добавить небольшое количество солей или мыла, то скорость охлаждения изменится. Для достижения одинаковой твердости на закаленной поверхности необходимо поддерживать температуру охлаждающей жидкости 20 – 30 градусов. Не следует часто менять воду в баке. Совершенно недопустимо охлаждать изделие в проточной воде.
Недостатком водяной закалки является образование трещин и коробления. Поэтому таким методом закаливают изделия только несложной формы или цементированные.
При закалке изделий сложной конфигурации из конструкционной стали применяется пятидесятипроцентный раствор соды каустической (холодный или подогретый до 50 – 60 градусов). Детали, нагретые в соляной ванне и закаленные в этом растворе, получаются светлыми. Нельзя допускать, чтобы температура раствора превышала 60 градусов.
Закалку легированной стали производят в минеральных маслах. Кстати, тонкие изделия из углеродистой стали также проводят в масле. Главное преимущество масляных ванн заключается в том, что скорость охлаждения не зависит от температуры масла: при температуре 20 градусов и 150 градусов изделие будет охлаждаться с одинаковой скоростью.
Следует остерегаться попадания воды в масляную ванну, так как это может привести к растрескиванию изделия. Что интересно: в масле, разогретом до температуры выше 100 градусов, попадание воды не приводит к появлению трещин в металле.
Отпуск.
После того, как материал подвергли закаливанию, производится его отпуск. Отпуск производится с целью придания стали высокой пластичности и снижения хрупкости с сохранением прочности. Он заключается в нагреве детали до температуры от 150-260 до 370-650 С, после чего производится медленное остывание.
Он может быть следующих видов:
• низкотемпературный, проводимый до 250 С для деталей из низколегированных и углеродистых сталей. Все металлорежущие и измерительные инструменты подвергаются низкотемпературному отпуску;
• среднетемпературный, проводится при температуре 350-500 С. Его проводят для пружин, штампов и рессор. После отпуска детали охлаждают в воде. Такой способ значительно увеличивает срок службы пружин;
• высокотемпературный. Он проводится при температурах в 500-680С и дает возможность для сохранения высокой прочности, вязкости, а также пластичности. Применяется для валов и зубчатых колес.
Самое важно при закалке металла это четкое соблюдение технологии.
Любой отклонение в сторону приводит к нежелательным последствиям.